- Докладчик: Хандогий Н.В., Соколова Е.В.
- Тема: Переход на магнетронный способ напыления алюминия на МДП структуры, технические и технологические решения.
- Организация: АО «НПП «Элар»
Вакуумное напыление тонких пленок алюминия является одним из основных технологических процессов изготовления различных типов полупроводниковых приборов и ИС. До настоящего времени основным методом вакуумного напыления пленок алюминия при производстве фоточувствительных приборов с зарядовой связью в АО «НПП «ЭЛАР» являлся термического (резистивного) испарения в вакууме. При относительно неплохой воспроизводимости данного процесса на технологическом оборудовании предприятия, имеется ряд проблем, которые препятствуют дальнейшему совершенствованию технологии.
Исходя из литературных данных и опыта практической работы предприятия, к материалу металлизации для п/п приборов и ИС предъявляется обширный набор требований [1].
К сожалению, в природе не существует металла, который бы идеально удовлетворял всему набору требований, но наиболее полно им отвечает высокочистый алюминий (чистотой не хуже 5N8 (99,9998%)), а также алюминий с небольшими добавками Si и/или Cu.
Вследствие своей высокой пластичности алюминий выдерживает возникающие из-за разности ТКР А1 и Si (которые равны, соответственно, 23,6∙10-6 и 3,3∙10-6 K-1) значительные внутренние напряжения [1].
В текущем производстве АО «НПП «ЭЛАР» напыление пленок алюминия осуществляется методом термического вакуумного напыления (резистивным способом). Данный способ обладает рядом технологических недостатков, которые неоднократно обсуждались в различных литературных источниках. В частности, этот процесс относительно сложно поддается автоматизации и требует высокого мастерства оператора напылительной установки.
Напылительный узел и планетарный механизм вращения подложек установки Alcatel EVA-600 показаны на рис. 1.
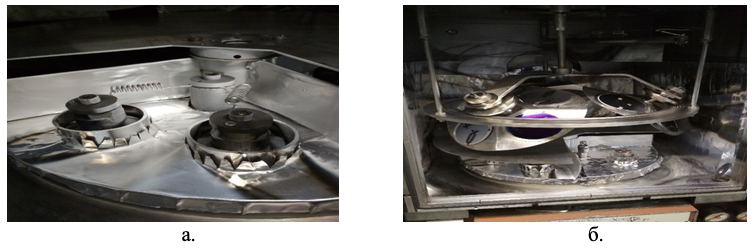
Говоря об основных недостатках термического (резистивного) способа напыления металлических покрытий, их можно разделить на технические и технологические. К техническим недостаткам можно отнести:
- Низкую технологичность и высокую трудоемкость изготовления спиралей, с учетом хрупкости используемого материала (вольфрама). Для изготовления спиралей требуется специальная оснастка, отдельное рабочее место и разработка отдельного технологического процесса.
- К чистоте вольфрама предъявляются довольно высокие требования. Так, наличие примесей щелочных металлов в концентрации более 0,001% может привести к увеличению темновых генерационных токов в приборных структурах и появлению нестабильности электрофизических характеристик.
На рис.2 показаны чистая (новая) спираль и аналогичная спираль после 6-ти процессов напыления, после чего их меняют.
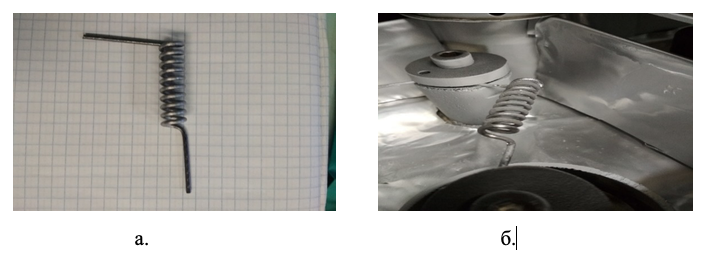
К технологическим недостаткам можно отнести:
- Возможность «скатывания» расплавленного алюминия к краям спирали, или падения капель алюминия из витков спирали, что приводит к увеличению времени распыления навески в первом случае и к уменьшению итоговой толщины пленки алюминия во втором случае.
- Из-за высокой скорости испарения алюминия пленка растет с высокой скоростью (пленка толщиной 0,5 микрометра формируется в течение 8-10 минут при распылении 4-х навесок из 2-х спиралей). Cложно обеспечить управление микрокристаллической структурой (степенью зернистости) алюминиевой пленки.
- У Al и Si давления насыщенных паров при температуре испарения алюминия, по литературным данным, имеют разницу в 3-4 порядка величины, что делает невозможным применение навесок алюминия с добавлением Si.
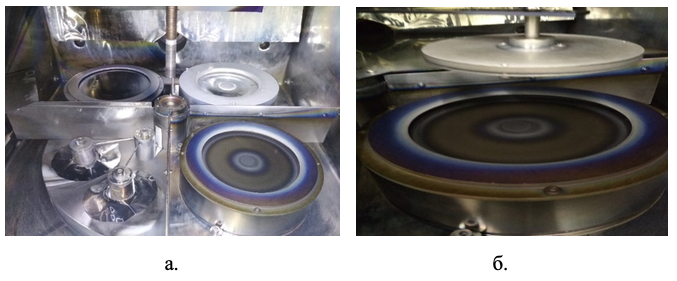
Для решения вышеперечисленных проблем предпринята разработка технологии напыления алюминиевых покрытий магнетронным способом. В процессе работы проведена модернизация технологической установки, вакуумная система откачки напылительной камеры заменена на безмасляную. Установлены магнетроны, рис. 3 а., способные работать как в ВЧ режиме (RF), так и в режиме постоянного тока (DC). В процессе работы опробованы алюминиевые мишени 2-х типов: чистый алюминий степени чистоты 6N и алюминий чистоты 5N8 с примесью 1%Si.
Магнетронный способ напыления предоставляет более широкий спектр возможностей управления технологическим процессом.
- Дополнительная очистка поверхности подложек в плазме разряда. Испарение алюминия с поверхности мишени более мелкими фракциями, нежели при резистивном испарении. Меньшая скорость осаждения металла положительно влияет на адгезию алюминия. Возможно использовать более низкие температуры нагрева подложек при предварительном обезгаживании и в процессе напыления алюминия на подложки, снижается термическое воздействие на обрабатываемые МДП структуры.
- Работа в относительно широком диапазоне рабочих давлений плазмообразующего газа, в совокупности с возможностью изменения мощности разряда в пределах 20-30% позволяет отработать стабильный, хорошо контролируемый технологический процесс, обеспечивающий управление зернистостью пленки алюминия и скоростью роста пленки.
- Магнетронный способ распыления рабочего материала мишени позволяет работать с алюминиевыми мишенями с добавлением различных материалов, в частности кремния, что позволяет исключить растворение кремния в слое пленки алюминия в области контактов, и как следствие, снизить образование «ямок травления».
- Возможность остановить и продолжить процесс напыления на любом этапе, использование «сухой» откачки, проведение непрерывного процесса напыления (без необходимости переключения между спиралями) позволяет исключить образование прочной, хотя и тонкой пленки Al2O3 между слоями алюминия.
- Использование планарного механизма вращения подложек, рис. 3б, вместо планетарного, показанного на рис. 1б, изменение расстояния от подложки до мишени в широких пределах (до 30 см), позволило добиться равномерности толщины пленки по диаметру подложки в пределах 3-4%. Время напыления пленки толщиной 0,5 мкм не превышает 35 минут.
- Изготовление мишеней требуемой конфигурации, степени чистоты металла и с необходимыми примесями, не представляет технической сложности.
- Замена мишеней производится только после полной выработки предыдущей мишени. Для контроля качества мишени достаточно произвести измерение вольт-фарадных характеристик тестовых МОП-структур с напыленными алюминиевыми электродами.
- Конструкция магнетронов позволяет работать при давлении в камере порядка (2÷6)·10-3 мбар (0.2÷0.6 Па).
Одним из основных требований при разработке процесса было получение электрофизических характеристик МДП-структур не хуже, чем получаются при «резистивном» способе испарения. Качество структур оценивалось по C-V характеристикам МДП-структур.
Из рис. 4 видно, что вольт-фарадные характеристики покрытий, полученных магнетронным способом, практически не отличаются от характеристик покрытий, полученных резистивным способом. Небольшой сдвиг C-V характеристики в сторону положительных напряжений для «магнетронной» структуры, свидетельствует о меньшей величине встроенного заряда, что может объясняться, в частности, отсутствием примесей щелочных металлов, наличествующих в вольфраме, из которого изготавливаются спирали. Анализ электрофизических параметров полученных покрытий в сравнении с резистивными пленками алюминия проводился по нескольким параметрам, в том числе и по времени жизни неосновных носителей, однако ограниченный объем настоящего доклада не позволяет привести все полученные данные.
Одним из требований, предъявляемых к пленкам алюминия является минимальная взаимная диффузия на границе раздела Al–Si. Растворимость Si в Al по массе достаточно велика: 0,25% при Т= 400K и 0,8% при 500K. В этом диапазоне температур коэффициент диффузии Si в тонкие пленки Al примерно в 40 раз выше, чем в объемный Al, что объясняется тем, что диффузия Si в тонких пленках Al идет главным образом вдоль границ зерен.
За счет растворения Si в Al в приповерхностной области кремния в контактных окнах возникают микропустоты, заполняемые за счет встречной диффузии атомов алюминия, причем возможно проникновение при термообработке Al внутрь контактных окон на глубину более 1 мкм. Если на участках контакта есть диффузионный переход с глубиной менее 1 мкм, может произойти замыкание перехода. Для исключения такого типа отказов переходов в Al добавляют в небольшой концентрации (обычно 0.5–1%) Si [2].
Рис. 4. Сравнение C-V характеристик магнетронного и резистивного способов напыления, 1,2 -–диэлектрик SiO2, 3,4 – диэлектрик Si3N4
Рис. 5. Фотографии размеров зерна на структурах, полученных в повторяющихся процессах резистивного напыления с интервалом в 10 процессов
Следующей важной характеристикой качества напыляемых пленок является их микрокристаллическая структура, характеризуемая размером зерна. Управление размером зерна пленок алюминия является одной из важных технологических задач в производстве МДП структур. Процесс резистивного напыления алюминия, несмотря на то, что он имеет в целом хорошую технологическую воспроизводимость, но степень контроля размера зерен достаточно ограничена. На рис. 5 показан разброс размеров зерна пленки алюминия при резистивном напылении (при одинаковой мощности источника питания и времени напыления). В противоположность этому, процесс магнетронного напыления позволяет, изменяя параметры разряда, такие как давление рабочего газа, расстояние от подложки до мишени, мощность разряда, в определенных пределах управлять размером зерна напыляемых пленок алюминия. Результаты представлены на рис. 6.
Рис. 6. Пленка алюминия 1напылена при мощности разряда на 20% меньше, чем пленка 2, остальные условия полностью совпадают.
Продолжается работа по совершенствованию процесса магнетронного напыления алюминия, направление дальнейших исследований сосредоточено на применении пленок алюминия с добавкой кремния (Al 5N8+1%Si) с целью уменьшения эрозии кремния (образования ямок травления) в сравнении с резистивным напылением.
Выводы: на основе результатов проведенных исследований установлено, что переход с резистивного на магнетронный способ напыления алюминия позволяет решить ряд технологических проблем и обеспечить улучшение качества изготавливаемых приборов и повышение выхода годных.
Список литературы.
- О.Д. Парфенов. Технология микросхем //М., Высш. школа, 1986, стр. 82-83.
- Б.С. Данилин. Применение низкотемпературной плазмы для нанесения тонких пленок //М., Энергоатомиздат, 1989, стр. 13.